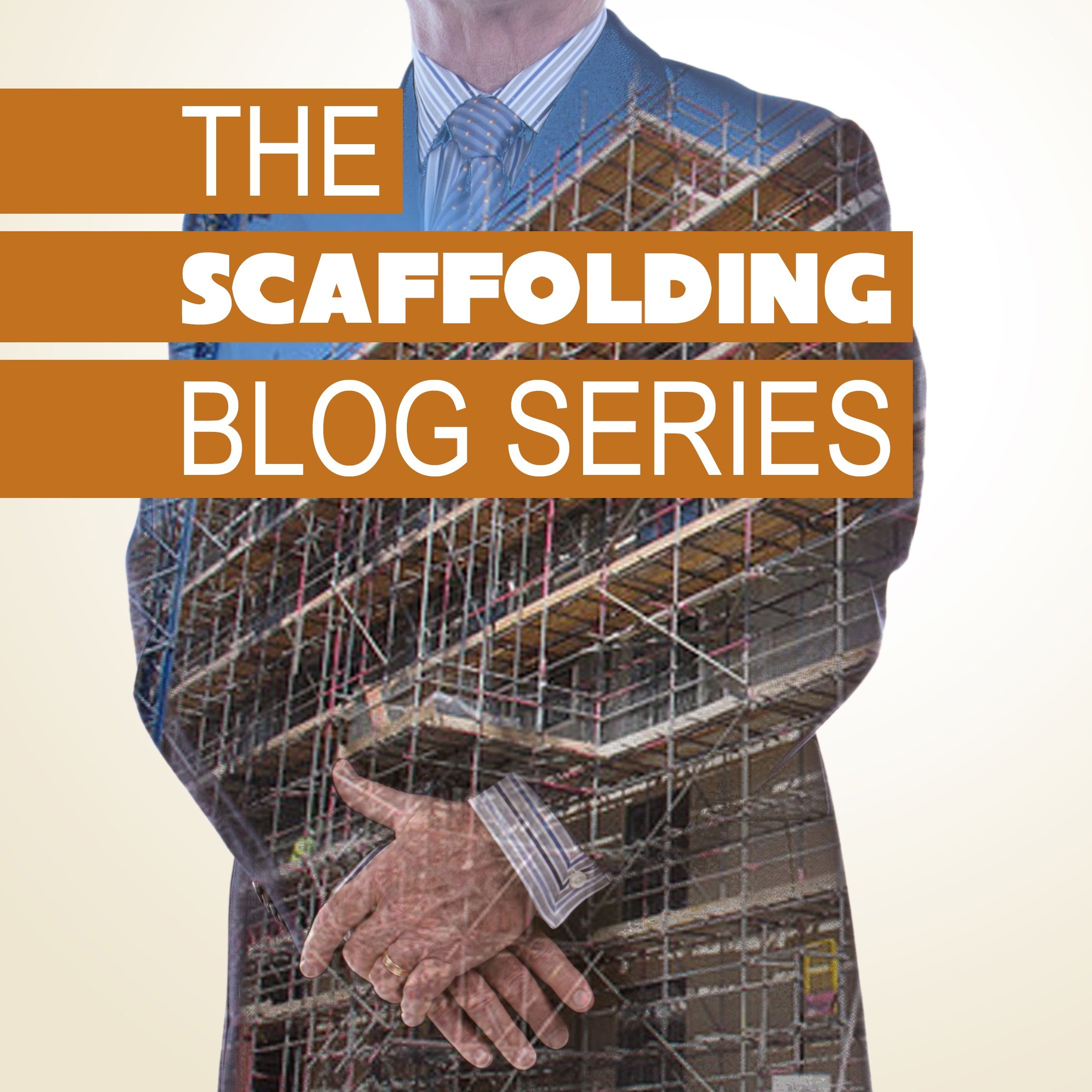
Job Costing Reports
Job Costing is like the weather…Everybody talks about it, but nobody wants to do anything about it. Job Costing in the construction industry is fundamental to most trades. Any successful contractor routinely tracks his costs on every job and compares them to the price he is getting for his work. But not scaffolding companies. I have seen the inside workings of many companies in the industry, and while some of them claim to track and document the costs of the jobs they perform, I have rarely seen a company that does it effectively.
Even at Safway it took years to put a company-wide job costing procedure in place. When we finally did, most of our managers thought the system was too complicated to use on a daily basis. A few of our best branch managers used a simple spreadsheet to track their largest jobs, but the data they used came from weekly job reports from their Construction Manager or Crew Foremen rather than actual payroll data.
What is a Job Cost Report?
Let’s define what a Job Cost Report actually is. In its simplest form, it is a report that tracks the ongoing cost of a construction project. Some JC reports only add up the costs after a job is completed, and that can be helpful in identifying problems to avoid on future jobs. But it is a lot more helpful if the report tracks job costs on a weekly basis so that problems can be identified and corrected before they get out of hand.
Why Are Job Cost Reports Valuable?
As I mentioned, accurate Job Costing can help identify problems during a job and after it’s complete, problems like an error in the equipment count needed to finish a certain elevation, or an access point that was missed in the take-off.
But an accurate JC Report can help you sort out a range of other problems. For example, it can tell you whether a low profit month or quarter is the result of one particularly bad job, or a general downward trend in pricing in a market. It can identify a crew that continually performs above or below budget, or a sales rep or estimator that needs to improve their performance. Actually, the ability to determine what a job costs and whether it was profitable is the basic skill that every manager of a construction company needs to possess.
Use Your Job Cost Report to Compare
An effective JC report also compares actual to budgeted costs. In other words, it compares periodic costs against a pre-determined budget to assist the project manager in determining whether the job is on schedule. This pre-determined job budget is actually the estimate and quotation for the job that your sales department developed.
In other words, it doesn’t do much good to track the cost of a job if you don’t have a detailed estimate of the job that includes details of what you have been hired to do. These details need to include hours to erect, hours to dismantle, the labor rate used in the estimate, the take-off, an equipment list, rental rate, job duration, a list of anticipated hard costs, customer requirements, special job site conditions, etc.
What Should a Job Cost Report Measure?
There are only a few cost categories on a scaffolding job.
- Labor Hours and Payroll Dollars
- Benefits
- Equipment Rentals
- Hard Costs
Labor – Tracking labor hours and cost is really the most important part of Job Costing. If your payroll is automated or handled by an outside payroll service (ADP, Paychex), this data is pretty easy to obtain. A manual system is another story. Either way, though, the major obstacle to tracking this data by job is getting your employees to code the hours they work to a specific job number on their time card. Most payroll services can keep track of hours and Payroll $ by job number, and give you a weekly report on it.
If the job coding on their time cards is not accurate, your JC reports won’t be either. This is easier said than done, especially in a growing company that is adding new scaffold builders, juggling crews, and hustling to meet the needs of new customers on lots of jobs. One common response to a new policy of coding time cards and hours by job number is for the erectors, crew foreman, or Superintendent to fill in the data of their workers at the end of the week, rather than on the day the work is done. This practice invariably ends up with guestimates and otherwise inaccurate date, and as they say, garbage in garbage out.
Employee Benefits – The problem with tracking the cost of benefits for your JC reports, is that they don’t appear on your weekly payroll records. The cost of health care, vacations, sick leave, etc. are an accounting function that at best gets calculated at the end of the month. But it is a cost that you’re incurring every hour that one of your scaffold builders spends on the job. So really the only way to calculate the cost of benefits is to come up with an estimate expressed as a percentage of the hourly wage, like 15 or 20%.
Equipment Rentals – There’s really no cost here, but you should know whether any job is using more or less equipment than originally estimated. The easiest way to do this is to require a detailed load list for the job from your sales dept before you start the job, and then periodically pull a net list of equipment currently on the job (deliveries less returns).
Hard Costs – hard costs include forklift rentals, crane time, outside trucking, maybe even re-rentals (if not counted against your own cost of equipment rentals), and any other out-of-pocket expense on a job. The importance of keeping track of these costs is second only to labor tracking. This source of this information is your Accounts Payable Administrator, who can provide you with weekly or monthly summaries of AP by job number, as long as your invoices and cash/CC receipts are coded to the same job number that your crews use.
It should be obvious at this point that producing an accurate and useful JC report is not just an accounting exercise. It ultimately requires the cooperation of nearly everyone in the company or at the branch. There is a role for the sales team, your crews, Payroll, AP, and Yard/Warehouse team.
Finally, if you decide to start tracking the cost of your jobs My suggestion is that you start slow, pick one job and focus on collecting the information on only that job. Once you and your team become familiar with how the numbers fit together, you can develop your own way to make Job Costing an integral part of your business.